High-pressure water jet cutting
The basis of this method is the grinding of divided material by the pressure of a water jet. The beam is created in a cutting head ending in a nozzle. When processing soft materials, we use a clean water jet, for other cases, an abrasive jet must be used. A suitable admixture is a natural abrasive - garnet. The divided material is not subjected to force. The cutting edge is not affected by heat in any way, it is always a cold cut. This fact is very important and also decisively distinguishes the water jet from other technologies for cutting materials, especially laser and microplasma.
Material examples:
-
structural, stainless and tool steel, aluminium, titanium, copper, zinc and nickel alloys, fiberglass, Kevlar, pertinax, plastics, foam plastics, ABS, Silon, sealing materials, Teflon, exp. graphite, industrial ceramics, ceramic tiles, glass, marble, granite, sandstone, carpets, PVC, cork, etc.
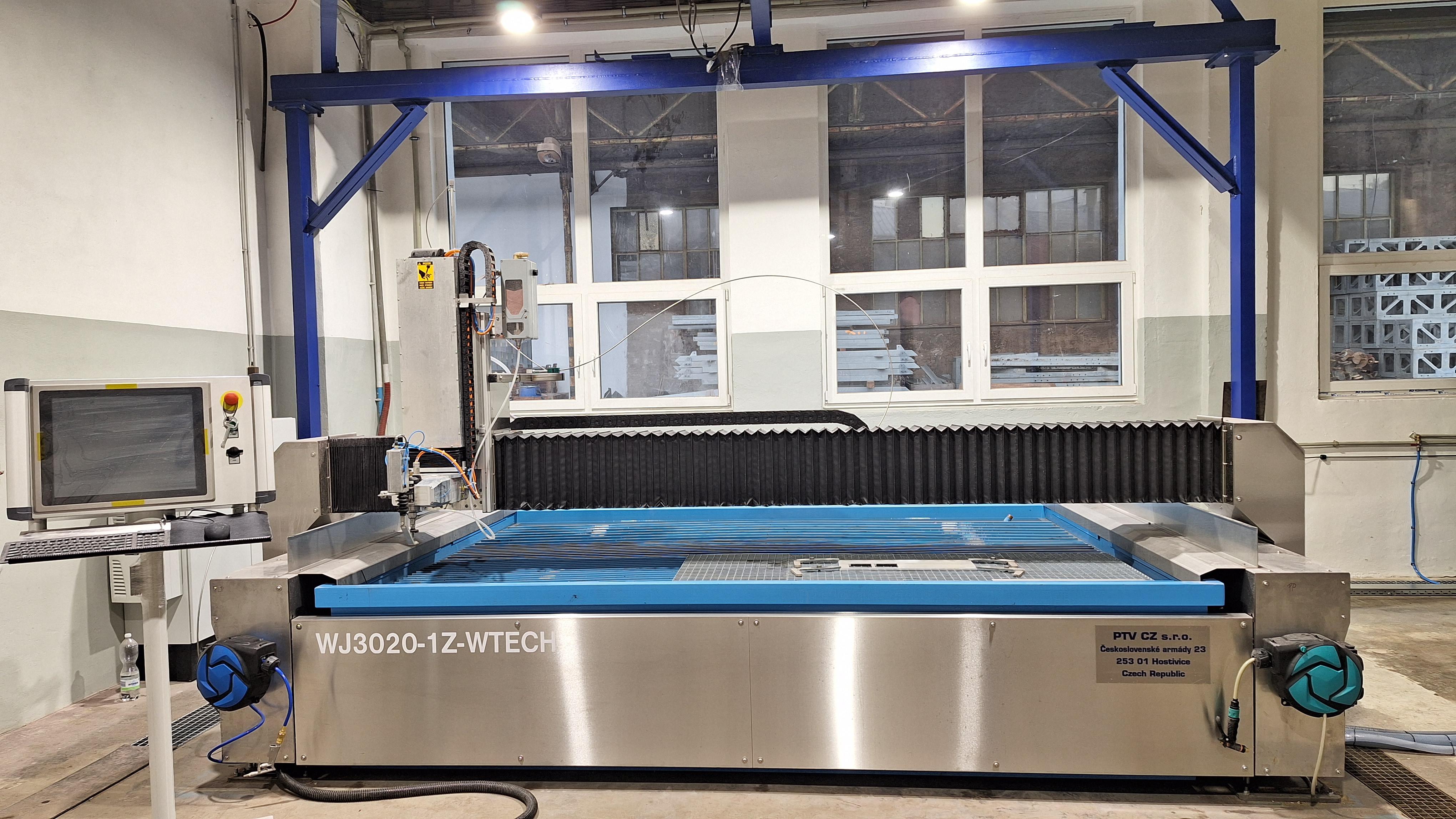
Water jet Uni Jet WJ3020-1ZWTECH
Technical parameters:
- Strength of divided material: 0,1 ÷ 200 mm
- Standard cut-out accuracy: +/- 0,1 mm
- Working area: 3 x 2 m
- Load capacity of the cutting grate: max. 150 kg / 1 m2
- Load capacity of the cutting bars: max. 500 kg / 1 m2
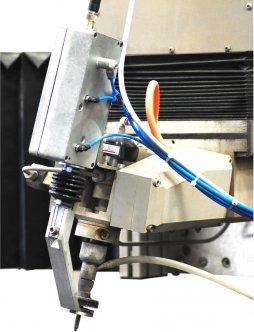
ProgressJet 5AX System
- fulfils all the functions of the standard ProgresJet system with lower accuracy and positioning dynamics
- is intended for the realization of 3D cut-outs from board blanks
- the mechanism enables tilting of the rotation axes within a range +/- 45°
- In 3D mode, requires program generated by 3D CAD-CAM (IGEMS module Bevel Cutting)
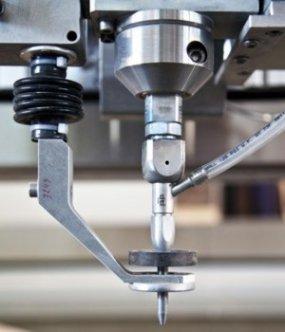
Height sensor
- The height sensor fulfils the function of automatically monitoring the optimal distance between the uneven cut blank and the cutting nozzle.
Advantages of water jet cutting
- cold cut, there is no thermal influence on the cut material and thus no structural changes
- minimal force effect of the beam on the cut material – microcracks do not occur
- universality – separates almost all materials, it is also possible to cut very difficult to divide and otherwise unmachinable materials
- the cut is burr-free, there is usually no need for subsequent processing, deburring and cutting of sharp edges
- the possibility of making even the most complex shapes in a single operation, including through holes and grooves
- a high utilization of the semi-finished product can be achieved thanks to the small diameter of the beam and the possibility of laying out several shapes on one semi-finished product, no harmful emissions into the air and no chemical action on the cut material
This machine is suitable for one-piece, small-batch and also high-volume production.